Преобразование мобильности требует целостного подхода
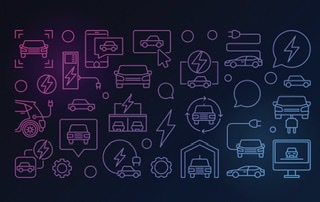
Широкий термин «трансформация мобильности» включает в себя новые бизнес-модели, политическую поддержку, новые городские концепции и многое другое. Важно принять эту сложность и интегрировать её в повседневную работу, независимо от вашей роли в автомобильной промышленности, считает Йозеф Вюнш, старший вице-президент BASF и руководитель исследований и разработок в области биополимеров, технологий поликонденсации и аддитивного производства, а также технологий переработки полимеров.
Когда электромобильность (e-mobility) обсуждается промышленниками и политиками, их дискуссии, как правило, сосредоточены вокруг аккумуляторных элементов и катодных активных материалов. Конечно, это «топливо» электронной мобильности, но для осуществления трансформации в автомобильной промышленности нужно решить гораздо больше задач. Например, это вопросы материалов, покрытий и охлаждающих жидкостей, которые являются движущей силой электромобильности.
Возгорание и распространение пламени на катодных металлах, вызванное высоким напряжением или коммутационной дугой, требуют использования материалов, легированных огнезащитными (FR) составами для разъёмов, оболочек кабелей или корпусов преобразователей переменного/постоянного тока на уровне, обычно не требуемом для двигателей внутреннего сгорания (ДВС). И многие другие части требуют агентов FR.
Поскольку трансмиссия электрифицирована, при разработке необходимо устранить тепловое расширение в шинах между металлическим проводником и пластиковыми проводами, а также смягчить звук электрического двигателя внутри. Шум, вибрация и жёсткость крепления двигателя и рамы должны быть изменены. Безопасность – прежде всего.
Кроме того, из-за дополнительного веса компонентов аккумуляторной батареи на борту амортизаторы требуют новой геометрии и сложных материалов, таких как лёгкие пенопласты, которые поглощают и распределяют энергию удара.
Опять же, для предотвращения воспламенения, а также для защиты стального корпуса от коррозии, вызванной электролитом, необходимы специальные материалы для покрытия аккумуляторного ящика. Аккумуляторный ящик покрыт специальной технологией e-coat с высокой рассеивающей способностью при малой толщине плёнки. Благодаря своему составу он экологически безопасен, так как требует более низкой температуры выпекания.
Оптимальный диапазон температур для зарядки и разрядки аккумулятора составляет от 35 до 40 °C. Необходимо разработать специальные охлаждающие жидкости с минимальным содержанием ионов и следов воды для управления температурой и с электромагнитным экранированием, т.е. электромагнитные волны не должны передаваться за пределы батарейного отсека.
Конечно, это также относится к необходимой инфраструктуре электромобильности – высоковольтным кабелям, силовым выключателям, силовой электронике, вилкам, охлаждающим жидкостям и т.д.
Развивающийся сегмент электромобилей несёт огромные возможности для инноваций в области химии, а не только батареи, что делает эту трансформацию такой увлекательной.
Создание автомобильных решений требует целостного взгляда на требования OEM к новым материалам, особенно когда речь идёт о взаимодействии компонентов электрической силовой установки и окружающих материалов.
Например, термопроводящая адгезия PU плохо прилипает к металлу или к полиэтиленовой пленке, которой обёрнут элемент батареи для изоляции. В таких случаях компании должны использовать правильные связи между группами экспертов в своей компании и специалистами своих поставщиков. Широкий портфель автомобильных решений и опыта позволяет производителям предлагать клиентам комплексный подход на 360 градусов.
Думать нестандартно – значит выходить за рамки вашей собственной компании. Сегодня компании должны развивать сотрудничество для создания эффективной и устойчивой автомобильной цепочки создания стоимости.
Трансформация, которую в настоящее время переживает автомобильная промышленность, ни в коем случае не является абстрактной. Это затрагивает отдельных специалистов, которые также должны приобретать новые знания.
Возьмем, к примеру, инженера по пластмассам из OEM-производителя, который разрабатывал материалы для ДВС. Теперь он или она могут оказаться в отделе аккумуляторных компонентов, занимаясь массовыми аспектами безопасности. Именно здесь вклад поставщика-партнёра выходит за рамки исследований и разработки, чтобы обеспечить поддержку для конкретных клиентов.
Автопроизводители придают большое значение ноу-хау, приобретённому поставщиками материалов за последние десятилетия, и их способности разрабатывать новые решения путём сотрудничества.
Подписывайтесь на журнал «Вестник ГЛОНАСС» и навигационный Telegram-канал